Shock-Tube Research
Shock tubes are impulse devices that generate a shock wave to instantaneously increase the temperature and pressure of a test section. The generated shock wave, which travels at supersonic speed (several Mach), can be tailored to create a wide range of temperature (500-10,000 K) and pressure (0.01-1000 bar) conditions. Shock tubes are typically implemented to study: (i) the impulse of shock wave on matter such as high-speed aerodynamics, blast waves, and material response; and (ii) the reacting flow behind the shock wave such as gas-phase reactions, fuel chemistry, and hypersonic reacting flows.
A shock tube consists of two long steel tube sections: a driver and a driven section. Before each experiment, a diaphragm is placed between the two sections. The desired test gas or tested object is then placed in the driven section. The driver section is then pressurized until the diaphragm bursts, creating a shock wave that travels through the driven section. This shock wave compresses and heats the gas in the driven section. When the shock wave reaches the end of the driven section, it hits the end flange and reflects back further compressing and heating the gas. This process occurs in a few microseconds to bring the tested gas from room temperature to a desired high temperature and pressure. Objects can also be placed at the end of the driven section to study their properties when encountering shock waves.
The KFUPM shock tube facility is intended to perform research related to the Interdisciplinary Research Center for Hydrogen Technologies and Carbon Management. This research can be classified into four themes: (i) reacting flows at combustion-like conditions towards clean energy applications (e.g., hydrogen and ammonia combustion), (ii) gas-phase processes related to hydrogen production (e.g., hydrocarbon pyrolysis and polygeneration processes), (iii) gas-phase reactions of carbon capture processes (e.g., Autothermal reforming process), and (iv) safety of energy storage systems (e.g., battery thermal runaway and fire suppressant chemistry). However, it should be noted that the shock tube is a versatile device that can be utilized for studying military applications. These include studying combustion of rocket and jet fuels, effect of blast waves on buildings and structures, high-velocity impact testing of protective armor and shelters, aerodynamic flows, and medical research related to injuries from blast waves and explosions.
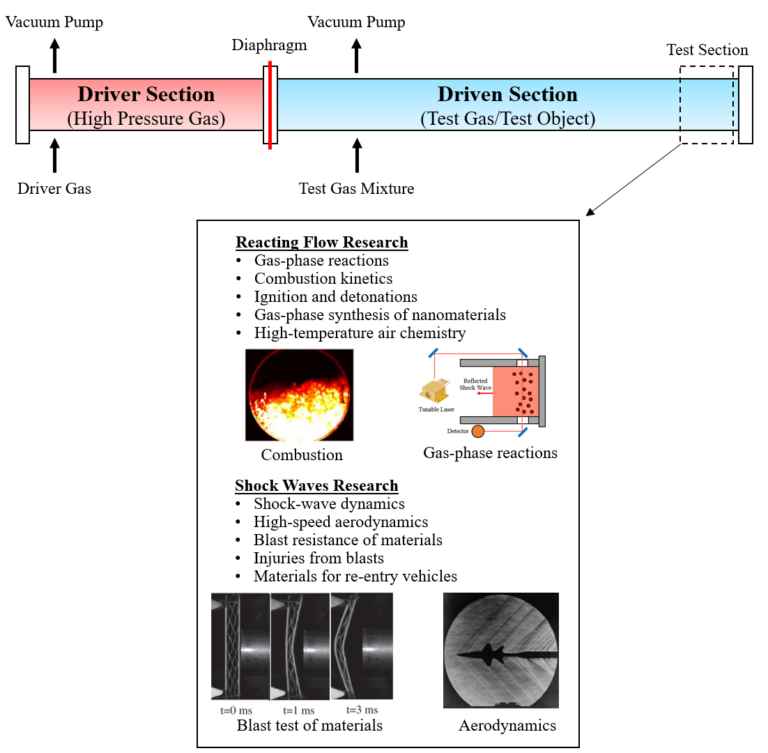
Simplified shock tube schematic and common research applications
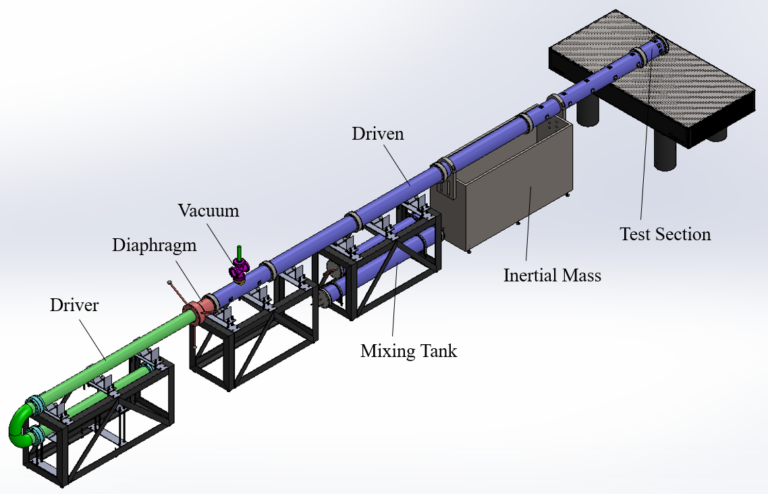
New KFUPM shock-tube facility (under development)
Laser-Based Sensors
In our group, we design and build custom-made laser-based sensor for detecting various gas molecules such as CO2, CO, H2S, NH3. Hydrocarbons, and many others through the use of Laser absorption spectroscopy (LAS). LAS techniques are a powerful and widely-used method for measuring flow-field parameters such as gas composition, temperature, velocity, and pressure. These techniques make use of the absorption of light by a particular gas, which can be used to determine the concentration of that gas in a sample. The absorption of light by a gas is a fundamental process that is governed by the laws of physics and can be used to measure a wide range of gases, including trace gases that are present in very low concentrations. The use of laser absorption techniques is prevalent in many fields such as environmental monitoring, industrial process control, medical diagnostics, and space exploration. This method is known for its high precision, accuracy, non-intrusiveness, high temporal resolution and low power consumption.
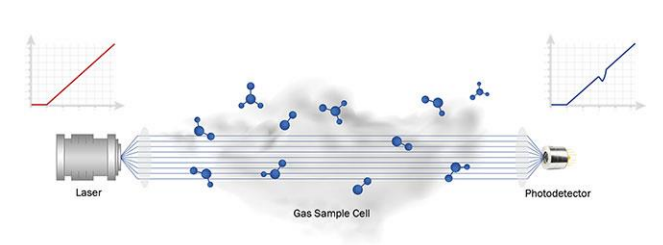
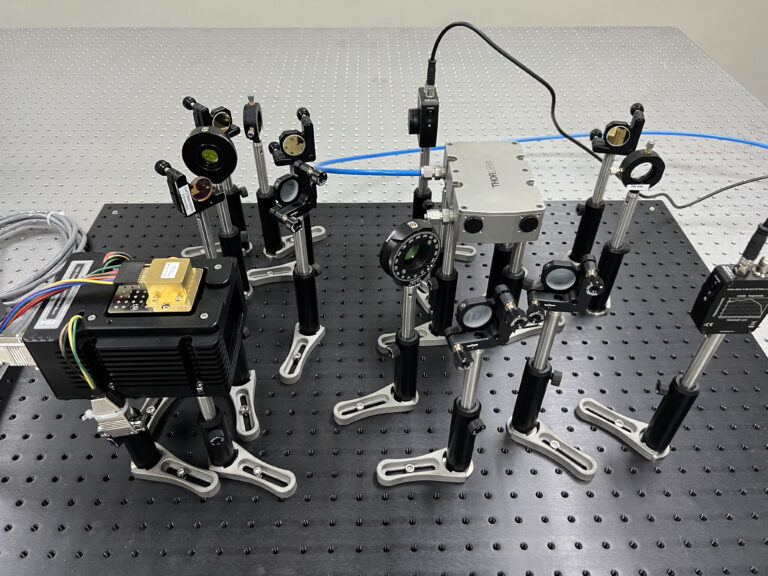